- Olwell Flutes
- Jan 18
- 2 min read
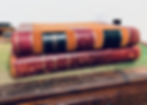
Greetings and Happy New Year, friends and flute fans! A little PSA here…
As we prepare to mark 50 years of making flutes (we aren’t quite sure how that happened, but wow!) we want to say a big “thank you” to our friends, customers, and music community for supporting us over the years and for providing so much encouragement and positive feedback. We do this for the joy of the music, and your goodwill lifts our spirits and reminds us of the importance of what we do.
Over the years, we have seen a steady increase in the number of keyed flute orders we receive, and as of this writing, our best guess has that wait-list at ten years or more, factoring in record numbers of orders each year from 2021-2024. This feels like quite the high-water mark, and after much discussion, we’ve decided to close our books to new keyed flute orders for the time being, effective as of this writing. We realize this is a big shift from having open books and taking all orders and we hate to disappoint eager flute players, but we hope folks can understand and appreciate the complexity we face with so many orders already in the pipeline. In trying to crunch the numbers, we realized that we were uncomfortable with the keyed flute list exceeding the ten year mark by too much, and we hope this will allow us to catch up a bit and focus on filling the orders we currently have before taking any more.
Please note that this change will only apply to keyed flutes—we will continue taking keyless orders and do our best to fill those requests in about a year. We made the decision some time ago to keep that list separate, as we wanted to be able to get some kind of flute into players’ hands without them having to wait longer than a year or two.
Patrick and Aaron continue to train our two apprentices (Aaron's brother Matthew and Seth Swingle), and we are hopeful that as they move from our informal apprenticeship program to our—equally informal—journeyman status, we will be in a position to increase production without sacrificing quality. If all goes according to plan, we hope to be able to meet that ten year estimate. In any case, to those already on the wait-list, please be assured that we are doing all we can to work our way down the queue, and of course, please email us via the contact page here if you have a question.
Anyhow, thanks to all for their custom and support, and stay tuned for announcements of celebratory 50th anniversary projects!
-Olwell Flutes
(Patrick, Aaron, and Matthew Olwell, and Seth Swingle)